Specialist Advice on What is Porosity in Welding and Exactly How to Resolve It
Specialist Advice on What is Porosity in Welding and Exactly How to Resolve It
Blog Article
Recognizing Porosity in Welding: Checking Out Causes, Results, and Prevention Techniques
As experts in the welding sector are well aware, comprehending the causes, results, and avoidance techniques associated to porosity is vital for achieving durable and trustworthy welds. By diving into the origin creates of porosity, analyzing its harmful effects on weld high quality, and checking out effective avoidance methods, welders can improve their understanding and skills to generate high-quality welds consistently.
Usual Causes of Porosity
Contamination, in the kind of dust, grease, or rust on the welding surface area, creates gas pockets when heated up, leading to porosity in the weld. Inappropriate shielding takes place when the securing gas, typically made use of in procedures like MIG and TIG welding, is not able to completely protect the liquified weld pool from responding with the bordering air, resulting in gas entrapment and subsequent porosity. Additionally, poor gas protection, frequently due to wrong flow rates or nozzle positioning, can leave parts of the weld unguarded, enabling porosity to develop.
Impacts on Weld Quality
The visibility of porosity in a weld can dramatically endanger the overall quality and integrity of the welded joint. Porosity within a weld produces voids or tooth cavities that weaken the structure, making it a lot more at risk to splitting, corrosion, and mechanical failure. These gaps act as tension concentrators, minimizing the load-bearing capability of the weld and increasing the likelihood of premature failing under used stress. Additionally, porosity can likewise work as potential websites for hydrogen entrapment, more exacerbating the degradation of the weld's mechanical homes.
Additionally, porosity can hinder the effectiveness of non-destructive screening (NDT) techniques, making it challenging to detect various other defects or discontinuities within the weld. This can lead to substantial safety worries, especially in critical applications where the architectural honesty of the welded components is vital.
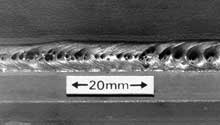
Avoidance Techniques Review
Provided the damaging influence of porosity on weld top quality, effective prevention methods are important to preserving the architectural honesty of welded joints. In addition, selecting the proper welding criteria, such as voltage, present, and take a trip rate, can help decrease the danger of porosity development. By integrating these prevention strategies into welding methods, the occurrence of porosity can be considerably decreased, leading to stronger and more reliable welded joints.
Value of Appropriate Protecting
Correct shielding in welding plays a crucial function in stopping atmospheric contamination and guaranteeing the integrity of bonded joints. Shielding gases, such as argon, helium, or a combination of both, are typically utilized to shield the weld pool from reacting with components in the air like oxygen and nitrogen. When these reactive elements come into contact with the warm weld pool, they can create porosity, leading to weak welds with minimized mechanical homes.

Poor shielding can cause numerous defects like porosity, spatter, and oxidation, compromising the structural stability of the welded joint. As a result, sticking to correct shielding methods is necessary to create top notch welds with minimal defects and make Clicking Here certain the durability and dependability of the bonded parts (What is Porosity).
Tracking and Control Methods
Exactly how can welders properly check and manage the welding process to ensure ideal Learn More Here outcomes and protect against problems like porosity? By constantly checking these variables, welders can identify deviations from the perfect conditions and make prompt modifications to protect against porosity formation.

Additionally, executing appropriate training programs for welders is essential for checking and regulating the welding process effectively. What is Porosity. Enlightening welders on the importance of keeping regular specifications, such as appropriate gas shielding and take a trip rate, can aid protect against porosity problems. Routine analyses and accreditations can also guarantee that welders excel in monitoring and regulating welding processes
In addition, making use of automated welding systems can boost monitoring and control abilities. These systems can specifically manage welding specifications, minimizing the chance of human mistake and making sure consistent weld top quality. By integrating advanced surveillance innovations, training programs, and automated systems, welders can properly monitor and regulate the welding process to reduce porosity issues and attain high-grade welds.
Final Thought

Report this page